Biodiesel as a Heavy Duty Low CO2 Solution
Save money with Low CO2 Biodiesel in your heavy duty fleet.
In Oregon the state ensures there is a cost associated with the CO2 intensity of a fuel. This is why Biodiesel is consistently lower cost than petroleum Diesel fuels on the West Coast. Get ahead of this curve and ensure your fleet benefits.
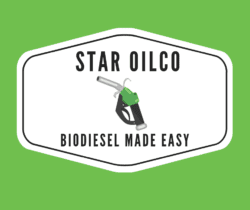
Why B99 Biodiesel was used in the past?
Prior to 2007 emission systems on modern diesels B99 Biodiesel was commonly used by fleets. The fact that Biodiesel is a domestic, renewable and low CO2 fuel with a benign tail pipe emission made it popular. B99 was the preferred fuel of dozens of fleets in the Pacific NW. After the EPA requirements starting in 2007 which added particulate traps, SCR, their dosing systems, and the general complexity of these clean diesel systems on modern diesels, B99 became problematic. Specifically the Tier 3 and Tier 4 diesel emission systems had a habit of choking on high blends of Biodiesel approaching B99. This issue has been solved by Optimus Technologies Vector System.
Why B99 Biodiesel is the solution for Heavy Duty Diesel fleets seeking a Low CO2 solution today?
The Optimus Technologies Vector System provides the solution by enabling two tanks of fuel. One tank dedicated to the diesel or R99 Renewable Diesel and the other tank dedicated to B100 or B99 pure Biodiesel. These systems optimize the systems of your modern Diesel fleet while also optimizing the performance and realities of the emission systems.
Star Oilco at the National Biodiesel Conference in Las Vegas
Mark Fitz, the President of Star Oilco, was invited to speak in front of a bunch of soy bean farmers on the subject of decarbonizing Heavy Duty diesel fleets. Below is a walk through of his view on where diesel fleets can go to cut their CO2 emission in half or more today. NOTE: Mark Fitz’s portion begins at 18 minutes.
Please reach out to Star Oilco if you have further questions about using B99 or other blends of Biodiesel to reduce your fleet’s operating cost while cutting CO2 emissions in half.
Contact Form