About Diesel Fuel
Bulk Diesel Fuel Frequently Asked Questions
Where your diesel comes from and what you need to know about ASTM Diesel Standards and ISO cleanliness code.
Where do Pacific Northwest vendors get their fuel?
In the Pacific Northwest, diesel is fungible. Everyone buys their fuel from each other in some way or another.
This means that every refiner is typically expecting to mix their diesel and gasoline products. The real difference is in the care a vendor takes to filter the fuel, additize and continuously check their fuel quality. If you are buying at the absolute lowest price possible, know that there is an incentive to skip any added value of quality assurance.
Through its Pacific Operations unit, Kinder Morgan operates approximately 3,000 miles of refined products pipeline that serves Arizona, California, Nevada, New Mexico, Oregon, Washington and Texas. With roots dating back to 1956, it is the largest products pipeline in the Western U.S., transporting more than one million barrels per day of gasoline, jet fuel and diesel fuel to our customers. The company-owned terminals also provide additional services, such as liquid petroleum product storage and loading facilities for delivery trucks.
Diesel Fuels
In the United States, diesel fuel is controlled according the American Society for Testing and Materials Standard D975-97. This standard describes a limited number of properties that diesel fuels must meet. It should be noted that the requirements are all performance- based. They do not mandate the composition of the fuel, only the specific performance related requirements demanded of a fuel for a diesel engine. The requirements of D975 are described below.
ASTM Specifications for Diesel Fuel Oils (D975)*
* You can go to the source of ASTM HERE if you have an interest in really getting in depth.
Diesel fuel is characterized in the United States by the ASTM standard D975. This standard identifies five grades of diesel fuel. We are only going to talk about the two most popular commercially diesel fuel used — No 1 and No. 2 diesel. The ASTM D975 standard is made up of a series of different tests that check the characteristic ranges of a fuel to confirm it is adequate to operate in your equipment. In simple terms, they are checking for specific gravity, the vapor point (when it turns into a gas), the flash point (when it catches fire), the dirt content, water content (how much microscopic entrained water), and a host of other requirements diesel must meet in order to be legal to be sold for use in your engine.
Grade No. 1-D and Ultra-Low Sulfur 1-D: This is a light distillate fuel for applications requiring a higher volatility fuel to accommodate rapidly fluctuating loads and speeds, as in light trucks and buses. The specification for this grade of diesel fuel overlaps with kerosene and jet fuel, and all three are commonly produced from the same base stock. One major use for No. 1-D diesel fuel is to blend with No. 2-D during winter to provide improved cold flow properties. Ultra Ultra-Low sulfur fuel is required for on-highway use with sulfur level < 0.05%.
Grade No. 2-D and Ultra-Low Sulfur 2-D: This is a middle- or mid-grade distillate fuel for applications that do not require a high volatility fuel. Typical applications include high-speed engines that operate for sustained periods at high load. Ultra-Low sulfur fuel is required for on-highway use with sulfur level < 0.05%.
Dealing with Dirty Fuel and Today’s Tier 4 Engines
Water and dirt are the biggest concerns for fuel quality. Why? Because no matter how perfect fuel is refined, these two elements can find their way into fuel and crash its performance. Water and dirt often build up in tanks just from the temperature change between night and day, causing a bulk fuel tank to breathe. Condensation and dust can also find their way into a bulk storage tank. If not addressed, they build up and will cause mechanical failures.
Dirty fuel will cause premature parts failure in equipment of any age. But newer equipment has far tighter tolerances than what we saw in previous decades. Today’s new and improved Tier 4 rail injector engines are more efficient, they burn cleaner, and run better, they are more powerful than ever before. But there are things that make fuel quality more important than ever. Because of the extremely high pressures (upwards of 35,000psi at the injector tip), the possibility of damage from dirty wet fuel is more prevalent than ever. This damage is much more pronounced in newer equipment with High Pressure Common Rail (HPCR) fuel systems. Hard particulate is commonly referred to as “dirt,” but is in fact made up of a wide variety of materials found at job sites (coal, iron, salt, etc.), generated by fuel tanks and lines (rust, corrosion, etc.) and inside engines (carbonaceous materials and wear particles).
Frequent diesel fuel filter changes — as well as the expensive, and time consuming, task of cleaning diesel fuel tanks — have become acceptable periodic maintenance, instead of a warning signal, for diesel engine failure. Diesel fuel filter elements should last a thousand hours or more, and injectors should endure 15,000 hours. However, since diesel fuel is inherently unstable, solids begin to form and the accumulating tank sludge will eventually clog your diesel fuel filters, ruin your injectors and cause diesel engines to smoke.
Symptoms
- Clogged and slimy filters
- Dark, hazy fuel
- Floating debris in tanks
- Sludge build up in tanks
- Loss of power and RPM
- Excessive smoke
- Corroded, pitted injectors
- Foul odor
The solids that form as the result of the inherent instability of the diesel fuel and the debris formed in the natural process of fuel degradation will accumulate in the bottom of your fuel tank. The sludge will form a coating or “bio-film” on the walls and baffles of the fuel tank, plug your fuel filters, adversely impact combustion efficiency, produce dark smoke from the exhaust, form acids that degrade injectors and fuel pumps, and impact performance. Eventually, fouled diesel fuel will clog fuel lines and ruin your equipment.
The Bigger Picture: ISO (International Standardization Organization)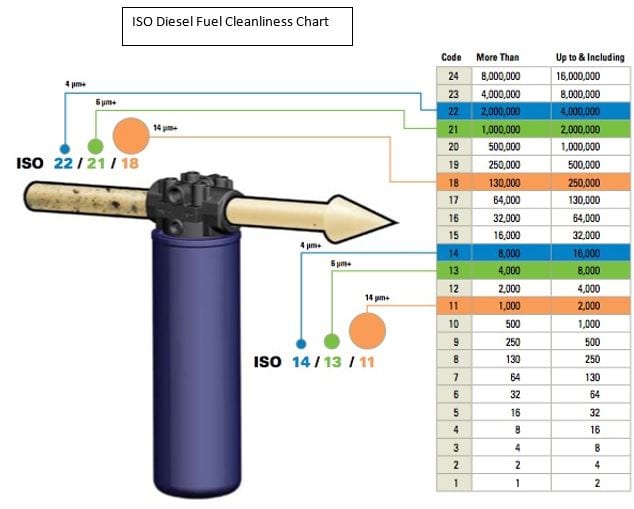
In today’s world, the definition of what constitutes clean or dirty fuel is critically important and, as such, fuel cleanliness levels are now measured and reported according to the ISO Cleanliness Code 4406:1999. The International Organization for Standardization (ISO) created the cleanliness code to quantify particulate contamination levels per milliliter of fluid at three sizes: 4μ, 6μ, 14μ. Microns.
Fuel Cleanliness vs. Engine Technology
Fuel cleanliness levels using the ISO4406:1999 method were officially documented as a global standard only as recently as 1998 with the development of the Worldwide Fuels Charter (WWFC). Since its inception, the charter has established a minimum cleanliness level for each of the diesel fuels under various available categories around the world.
Most mainstream engine OEM’s now subscribe to these standards. Interestingly (and somewhat troubling to note), however, is that fuel cleanliness levels as specified by engine OEM’s and the WWFC have not changed since their inception in 1998, despite the enormous advances in fuel injection technology. This relationship is best represented in the previous table that identifies the advances in fuel injection systems and clearly highlights how OEM’s and the WWFC have not responded to reduce fuel cleanliness in accordance with advancements in technology.
Diesel Fuel Injection – Advancing Technologies & Cleanliness Levels
This table identifies that, over time, fuel injector critical clearances have halved and fuel pressures have doubled, yet the level of fuel cleanliness being specified has not changed in accordance with such advancements. In fact, the same cleanliness levels specified in 2000 are still being used today despite these magnificent technological design advancements by engine manufacturers worldwide.
Leading fuel injector manufacturers around the world have clearly identified and communicated that they require ULSD fuels with ISO fuel cleanliness levels as low as ISO12/9/6 to maintain ultimate performance and reliability. It is here where we see an enormous mismatch in what the fuel injection OEM desires as a fuel cleanliness level, to what the engine OEM’s and the WWFC are advising the industry. The following table identifies the discrepancies in fuel cleanliness levels.
Diesel Cleanliness Levels
WWFC Diesel Category Fuel Cleanliness Standards
Damage Caused by Hard Particulate
Hard particulates cause problems with moving parts in the fuel system. This can lead to starting problems, poor engine performance, idling issues and, potentially, complete engine failure. All too common, hard particulates damage engines.
The spray pattern generated by the HPCR injector is critical for proper combustion and overall fuel system performance.
It must be extremely precise in terms of quantity, distribution and timing. Ball seat valves are sealed with balls that are only 1mm in diameter. A good seal is absolutely necessary for proper injection. Damage from erosive wear, such as shown below, will cause over fueling, leading to decreased fuel efficiency and eventually shut you down altogether.
Pump performance can also be compromised by scoring and abrasive wear. These issues are magnified by tighter tolerances and extreme pressures in HPCR engines. In these circumstances, it is the smallest particles (1-5 microns in size) that cause the most damage, virtually sand blasting part surfaces.
Allowable Levels of Hard Particulate
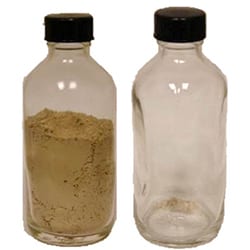
How Dirt Enters Fuel
Dust and dirt are all around us, especially on job sites. Diesel fuel is fairly clean when it leaves the refinery but becomes contaminated each time it is transferred or stored. Below you will find some of the key contributors of fuel contamination:
Pipelines: Most pipelines are not new, and certainly not in pristine condition. Corrosion inhibitors are added at most refineries to help protect pipelines, but rust and other hard particulate is nevertheless picked up by the fuel that flows through them.
Barges and rail cars: How often are they drained and scrubbed out? What was in the last load? Where did it come from? How much of it was still in the tank when your load was picked up? How long was it in transit? Is the tank hermetically sealed? There are many opportunities for contaminants to make their way into the fuel.
Terminal tanks: Terminal tanks usually see a high rate of turnover, so there is not much time for the fuel to pick-up contamination from outside ingress. Has the tank ever received a “bad load” from a pipeline or a barge? Has larger dirt had a chance to settle on the bottom of the tank? How often has it been cleaned out? Was it just filled? Did the bottom get churned up in the process? How full was the tank when your fuel was loaded into the delivery truck? There are many variables that can affect fuel cleanliness.
Delivery trucks: All the same issues that apply to stationary tanks also apply to tanker trucks, except that truck tanks never get a chance to settle. In addition, have you ever considered how much dirt gets into that tanker while it is delivering fuel to a customer, potentially a customer in an extremely dusty environment? As fuel flows out, air is sucked in to displace it. Is there anything protecting the inside of the tank from all the dust in the air? Generally not. Venting is typically completely unprotected, as seen in the image to the right.
Storage tanks: Onsite bulk storage tanks typically see less rapid turn-over than terminal tanks. In addition to those issues, yard and jobsite tanks can also develop serious problems with other sources of contamination, such as the ingress of dirt and water, condensation, rust, corrosion, microbial growth, glycerin fall-out and additive instability. Time and temperature become big factors affecting fuel quality.
Dispensing process: How far does your diesel need to travel between the bulk tank and the dispenser? The more pipe it runs though, the more potential there is for contamination. Are your dispenser nozzles kept clean? Are they ever dropped on the ground? Then what? What about the vehicles’ fuel tank inlets, are they clean? Think about the extremely tight tolerances in your fuel system, then take another look at housekeeping issues. You will see them through new eyes.
Onboard fuel tanks: Contamination continues even after the fuel is in the equipment. What has that tank seen in the past? Has it been left stagnant for long periods? What kind of protection is there on the equipment’s air intake vents? Heavy equipment does hard, dirty work.
Engines: Unfortunately, even if the fuel in your tank could be perfect, additional contamination is generated by the fuel system itself. Wear particles are created by mechanical friction. High heat and extreme pressure generated inside the modern engine, lead to coking and the creation of carbon products at the injector. Much of this internally-produced particulate is returned to the fuel tank, along with the unburned diesel.
The Bottom Line
No one gets special fuel, no one has better fuel, no one has cleaner fuel. Diesel fuel vendors get the same fuel, from the same pipeline, delivered to the same terminals. We all wait in the same lines with our tank trucks to get that same fuel. So ask yourself: Given that the fuel is the same, what sets one vendor apart from all the others? Star Oilco Premium Diesel fuel is treated with Hydrotex PowerKleen® additive running through Donaldson filtration systems.
FURTHER READING ON DIESEL FUEL:
Read about Star Oilco’s approach to Fuel Quality Assurance: Star Oilco – Precision Fuel Management
Read about dealing with biological growth in your diesel tank: Bioguard Plus 6 biocide treatment for diesel
Get Chevron’s Technical Manual to Diesel Fuel (essentially an easy to read text book on diesel): Chevron’s Fuel Technical Review
Get a white paper from Donaldson Filtration on tier 4 engines and fuel cleanliness: Donaldson on Tier 4 Engine Fuel Contamination
Read more about Donaldson Desiccant Breathers for bulk diesel tanks: Why use a Donaldson Desiccant Breather for a bulk diesel storage tank.